_____激光切割机作为目前行业内先进板材加工设备,在实际生产过程中,切割方法直接决定了生产效率和工件质量,因此探讨行之有效的切割技巧,以期提高生产效率和产品质量,降低板材浪费率显得十分必要。本文主要描述了几种已经在生产过程中得到充分验证的切割技巧,包括蛙跳式空行程进给、集中穿孔、微连接的应用以及在激光切割加工时穿孔点的优化选择。在实际的生产中,通过上述方法有效提高了工件的切割质量和加工效率。激光切割是一种高能量密度,可控性好的无接触加工,是利用从激光发生器发射出的激光束,经光路系统将激光束聚焦成最小直径可小于0.1mm 的光斑,达到高功率密度的激光束照射条件,激光的热量被照射的工件材料吸收后,工件温度急剧上升,到达熔点,材料开始液化并形成孔洞,并伴随着高压气流,随着光束与工件相对位置的移动,最终使材料形成连续切缝。切割时需要添加与被切割材料相适应的辅助气体,以加速材料的熔化,吹走熔渣并保护切缝不被氧化,从而达到优异的切割速度和切割质量。
其中,激光切割由于切口光滑、尺寸精确、速度快、噪声小、烟尘少以及能进行各种形状复杂的板材切割等优点,在16mm以下的钢板中,得到越来越广泛的应用。
而在激光实际切割过程中,切割技巧至关重要。因此,熟练掌握各种激光切割技巧,是提高生产效率的关键。通过试验探索,总结了以下几种激光切割中会用到的切割技巧,经过在实际生产中的运用,有效的提高了生产效率,减少了材料的浪费。
蛙跳式空行程进给
蛙跳是激光切割机的空程方式。如图1 所示,切割过程完成孔1 之后,接着要切割孔2。此时切割头要从点A 移动到点B。当然,移动过程中要关闭激光。从点A 到点B 之间的运动过程,设备“空”跑,称为空行程。
激光切割机一般空行程如图2 所示,切割头要次第完成三个动作:上升(到足够安全的高度)、平动(到达点B 的上方)、下降。
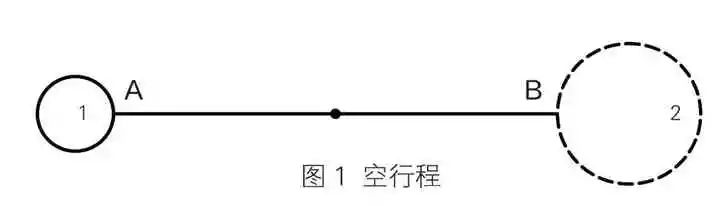
图1 空行程
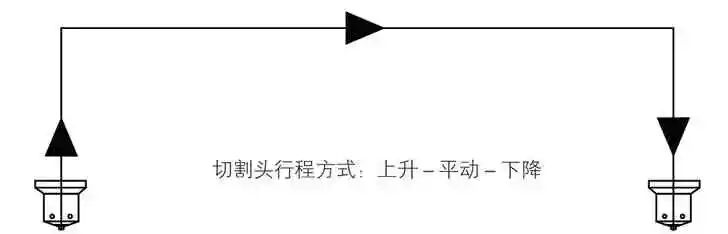
图2 切割头空行程方式
而压缩空程时间,可明显提高设备的效率。如果将次第完成的三个动作,变为“同时”完成,便可缩短空程时间,即切割头从点A开始向点B移动时,同时上升;接近点B时,同时下降,犹如蛙跳动作一样,如图3 所示。采用这种空行程方式,其只占用了从点A 到点B 平动的时间,省去了上升、下降的时间。激光切割机采用蛙跳的空行程进给,有效减少了空行程运动时间,加工效率便可有效提升。
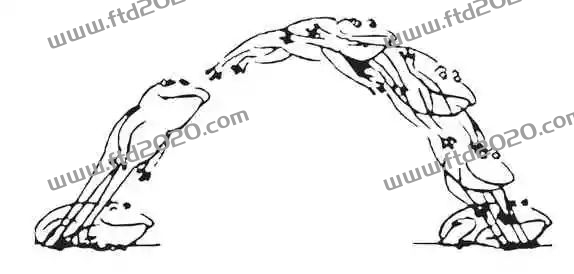
图3 切割头空程运动轨迹类似于蛙跳的弧线
集中穿孔
集中穿孔,也称为预穿孔,实际上是一种加工工艺,一般激光切割设备并无此功能。比如激光在切割较厚的板材时,每一个轮廓的切割加工都要经历穿孔和切割两个阶段。而常规的加工工艺为穿孔→切割轮廓1 →穿孔→切割轮廓2,如图4 所示,其中小圆点是穿孔点,箭头是切割路径顺序。
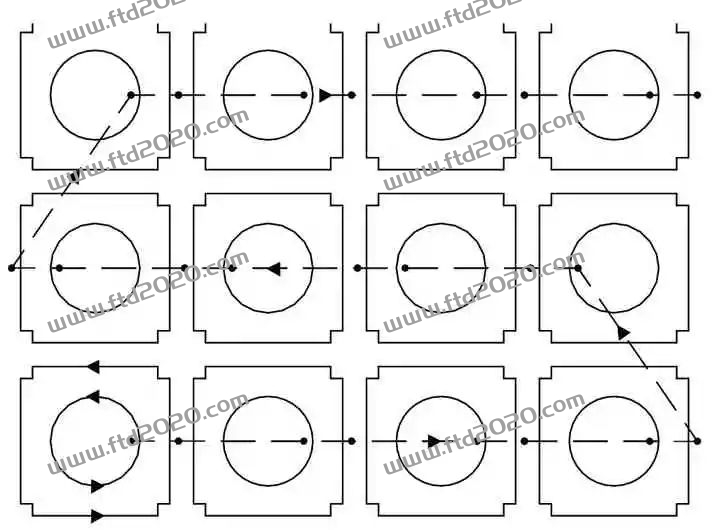
图4 常规激光切割加工路径
而所谓的集中穿孔,就是将整张板料上的所有穿孔过程提前集中执行,然后再执行切割过程,如图5 所示,图中小圆点是穿孔点,箭头是空行程路径顺序。
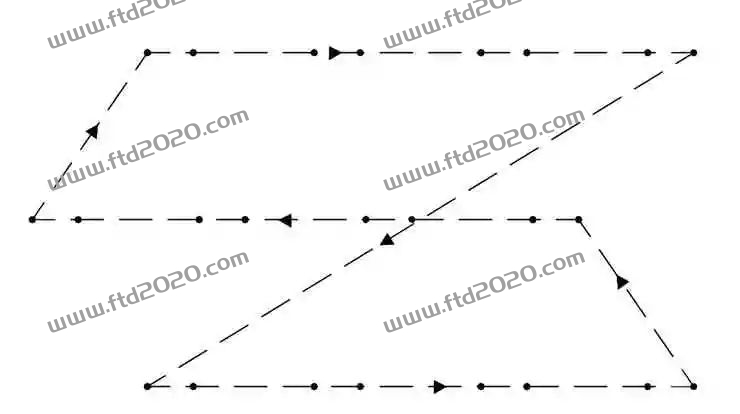
图5 集中穿孔加工工艺
集中穿孔的加工工艺路线为完成所有轮廓的穿孔→回到起点→切割所有轮廓。与常规加工工艺相比,集中穿孔时设备的运行轨迹总长有所增加,但其优点在于集中穿孔可有效避免过烧。尤其是在厚板穿孔过程中,在穿孔点周围形成热量聚集,如果此时紧接着切割,就会出现过烧现象(图6)。而采用集中穿孔工艺方式,完成所有穿孔、返回起点再切割,由于有充分的时间散热,就避免了过烧现象。
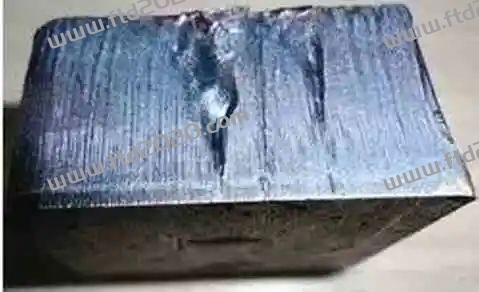
图6 切割面过烧现象
微连接的应用
激光切割在加工时,板料被锯齿状的支撑条托住,被切割下来的零件如果不够小,就不能从支撑条的缝隙中落下;如果不够大,就不能被支撑条托住,则可能失去平衡,发生工件翘起。而高速运动的切割头可能与之发生碰撞,轻则停机,重则发生损坏,如图7 所示。
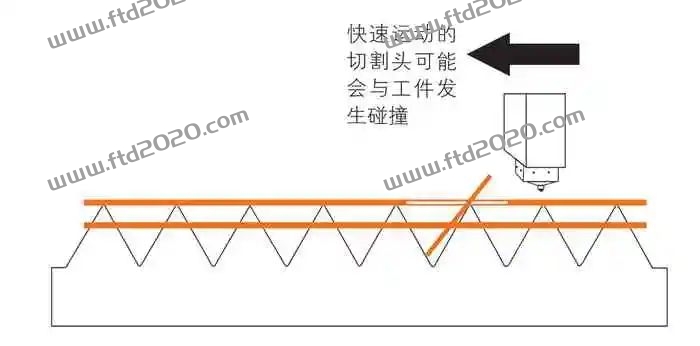
图7 切割头和翘曲工件发生碰撞
而采用微连接切割工艺,则可避免发生此类问题。具体方法为:在对图形进行激光切割编程时,有意将封闭的轮廓断开若干处,使得切割完成后零件与周围的材料粘连在一起,不致掉落,而这些断开处,称为微连接(图8)。断开的距离,约在0.2 ~1mm,需按照断开距离与板料的厚度成反比的原则来选取。
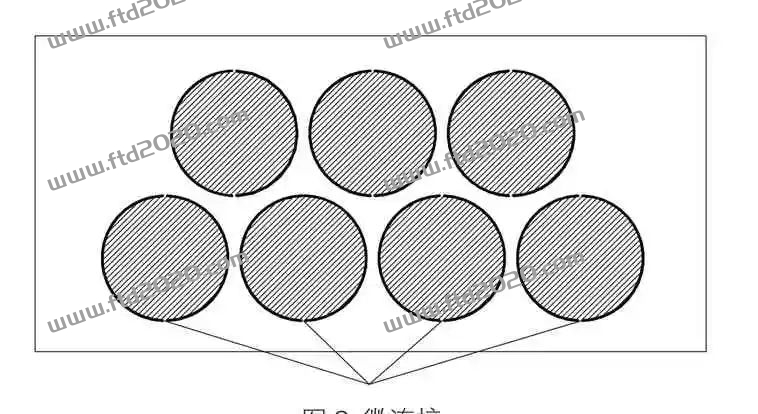
图8 微连接
在激光切割过程中使用微连接将零件与周围材料连在一起时,要根据轮廓的长度,添加合适数量的微连接;还要区分内外轮廓,使不留微连接的内轮廓(废料)掉落,而保留微连接的外轮廓(工件)与母材粘连在一起,从而免去分拣的工作。
切割小孔(直径小于板厚)变形情况的分析
(1)切割8mm 以内的碳钢类板材,孔径不能小于板材的厚度。
(2)切割10mm 以内的碳钢类板材,孔径不能小于板材厚度的1.2 倍。
(3)切割4mm 以内的不锈钢板材,孔径不能小于板材的厚度。
(4)切割4mm 以上的不锈钢板材,孔径不能小于板厚的1.2 倍。
然而在激光切割生产中,经常会遇到孔径小于板厚的工件,且加工困难,切割质量较差。主要是因为当程序切割到直径小于板厚的圆孔时,机床默认的切割方式由原来的连续切割变为脉冲穿孔式切割,这使得激光能量在一个很小的区域内过于集中,非加工区域也被烧损,造成孔的变形,影响加工质量。经过摸索和尝试,发现若使用熔化切割代替火焰切割,也就是当程序运行到切割小圆孔时,调整切割状态,用高压氮气代替氧气进行切割,当切割完小孔时,再变回的氧气切割。用这种方法切割出来的小孔,无论正反面圆孔形状均十分规则,可达到合格要求,并降低废品率,提高生产效率。
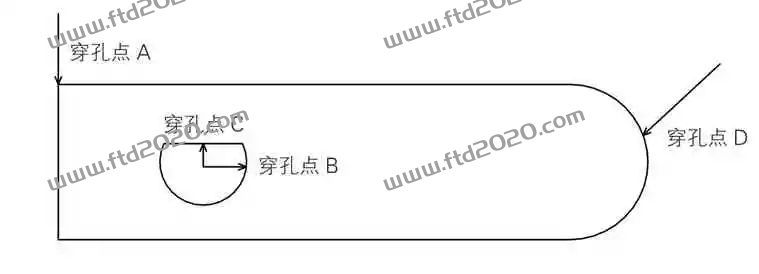
图9 激光切割加工时穿孔点的选择
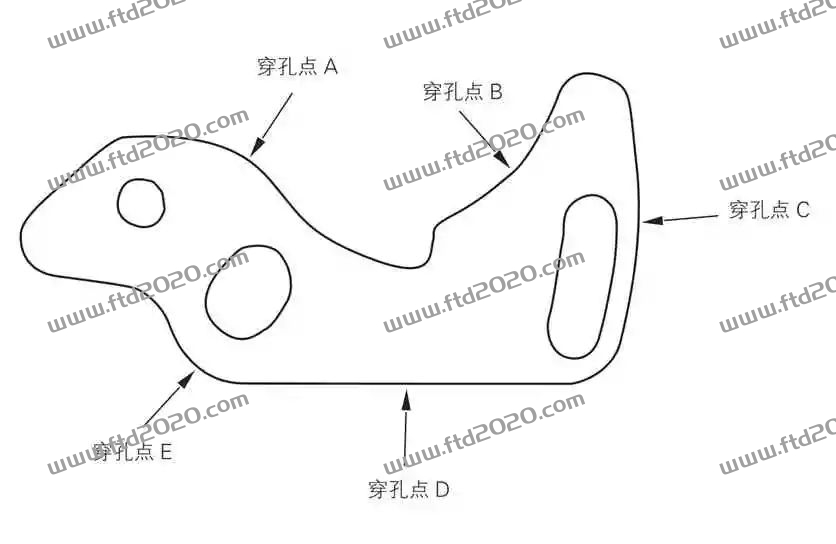
图10 激光切割加工时穿孔点的选择
激光切割加工时穿孔点的选择
在激光切割加工过程中,激光束在材料上连续照射后在中心形成一个凹坑,进而与激光束同轴的工作气流很快会将熔融材料去除,形成一个小孔。此孔类似于线切割的穿线孔,激光束以此孔为加工起始点进行轮廓切割,通常情况下飞行光路激光束的走线方向和被加工零件切割轮廓的切线方向垂直。
因此,激光束在开始穿透钢板时到进入零件轮廓切割的这一段时间,其切割方向上将有一个很大的改变,由垂直于切割轮廓的切线方向转为与切割轮廓的切线重合,即与轮廓切线的夹角为0°,这样就会在被加工材料的切割断面上留下比较粗糙的切割面,这主要是由于在短时间内,激光束在移动中的方向变化过快导致。因此在采用激光切割加工零件时,必须注意此问题。一般来说,在工件对表面切割断口没有粗糙度要求时,可以在激光切割编程时不做手动处理,让控制软件自动产生穿孔点;若所要加工的工件切割断面有较高要求,就必须进行穿孔调整,通常需要在编制激光切割程序时对激光束的起始位置做手动调整,即人工对于穿孔点控制。需要把激光程序原来产生的穿孔点移到需要的合理位置,以达对加工零件表面精度的要求。
如图9 所示,若此工件对圆弧部分有切割面粗糙度要求,在编制激光切割程序时,切割起始(穿孔点)就要设置在A 和C,而不能设置在B 和D。而如果此工件只对直线边切割面粗糙度有要求,那么在编制激光切割程序时,切割起始点就要设置在B 和D,而不能设置在A 和C。
同样的,如图10 所示,如果此工件外形设计对圆弧有精度要求,我们在编制激光切割程序时,切割起始点(穿孔点)就只能设置在D,而如果此零件只对直线边的精度有要求,那我们在编制激光切割程序时,切割起始点(穿孔点)就可以选择除了D 点以外的任何点了。
结束语
在实际生产过程中,激光切割机的操作复杂而又精细,工件种类繁多,材质多样,随着切割工艺的日益成熟,只要能够熟练运用各种切割技巧,并在不断的解决问题中积累经验,就可以提高人和设备的加工生产能力。
